What is FDM 3D Printing?
Hey innovators!
Welcome back to the Slicedog® Blog, where we break down the essentials of high-efficiency 3D printing.
Today, we’re diving into Fused Deposition Modeling (FDM)—the most popular 3D printing method. Affordable, versatile, and easy to use, FDM powers everything from prototyping to production. But how does it work, what are its limits, and how can you optimize it for your business? Let’s find out!
Description of FDM 3D Printing
Fused Deposition Modeling (FDM) is the most widely used method of 3D printing and a key part of additive manufacturing. Unlike subtractive manufacturing methods such as milling, turning, or grinding, which remove material to shape parts, FDM builds objects layer by layer using thermoplastic materials.
In FDM, the printer’s print head extrudes melted filament through a nozzle, depositing it precisely onto the print bed or the previous layer. The material cools and solidifies to form the final structure.
Compared to other 3D printing technologies like SLS (Selective Laser Sintering) or SLA (Stereolithography), FDM is simpler, more affordable, and heavily used by hobbyists. However, its practicality extends to industrial applications as well, making it ideal for prototyping and certain low-volume manufacturing tasks.
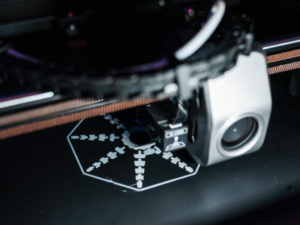
FDM 3D Printer laying hot thermoplastic material
Key Terms in FDM 3D Printing
To better understand FDM, here are some essential terms:
- Extruder: A mechanism that pushes filament into the hotend for melting and extrusion.
- Print Bed: The surface on which 3D prints are built. Heated beds improve adhesion for certain materials.
- Nozzle: The component of the extruder that melts and deposits filament in fine layers.
- Filament: The thermoplastic material used for FDM 3D printing, available in various types like PLA, PETG, and ABS.
- Firmware: The software controlling the 3D printer’s hardware.
- Slicer: A program that converts 3D models into printable layers and generates G-code for the printer.
- G-code: The programming language that instructs the 3D printer on movement and settings.
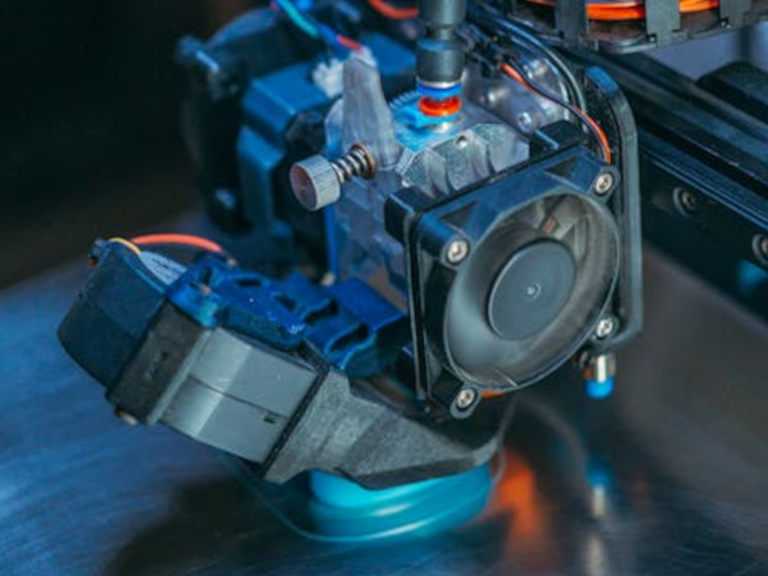
In the context of 3D printing, extruder is mechanism that pushes filament into the hotend
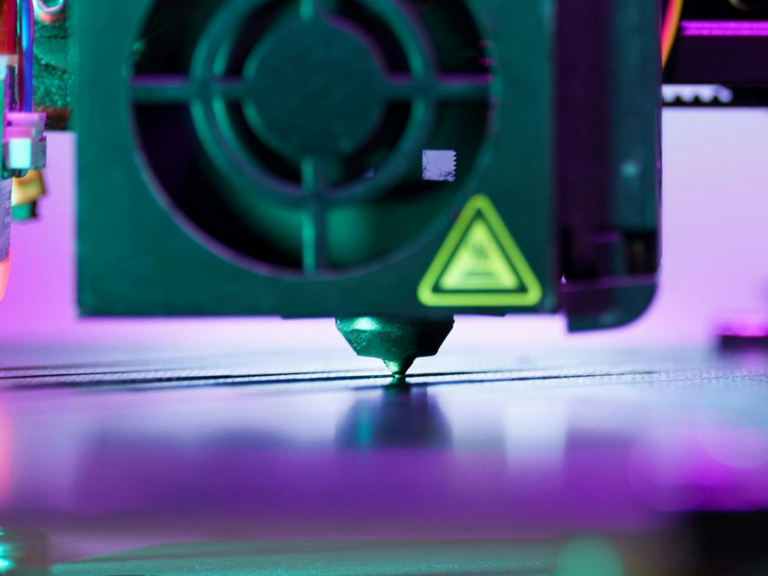
Nozzle is hot part of the 3D printer that lays down printed material
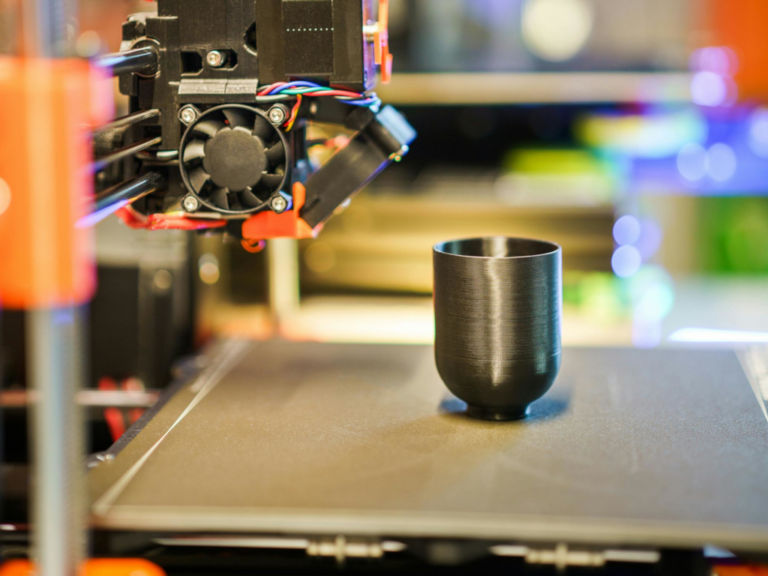
While printing first layer, print bed is crucial. Often heated for easier 3D printing
Common Materials for FDM 3D Printing
Choosing the right material is critical for achieving the desired properties in your 3D-printed part. Here are the most commonly used materials:
- PLA (Polylactic Acid)
- Characteristics: Easy to print, affordable, and biodegradable.
- Applications: Prototypes, decorative models, and low-stress parts.
- Limitations: Low strength and poor resistance to heat or outdoor conditions.
- PETG (Polyethylene Terephthalate Glycol)
- Characteristics: Stronger and more durable than PLA, with good weather resistance.
- Applications: Functional prototypes, end-use parts, and outdoor applications.
- Limitations: Slightly harder to print than PLA but still user-friendly.
- ABS (Acrylonitrile Butadiene Styrene)
- Characteristics: Durable and heat-resistant, with good chemical resistance.
- Applications: Automotive parts, tools, and industrial components.
- Limitations: Requires a heated chamber to avoid warping, making it challenging for hobby-grade printers.
- TPU (Thermoplastic Polyurethane)
- Characteristics: Flexible, impact-resistant, and abrasion-resistant.
- Applications: Phone cases, vibration dampers, and wear-resistant components.
- Limitations: Requires specific printer setups for consistent results.
- Nylon (Polyamide)
- Characteristics: High strength, flexibility, and wear resistance.
- Applications: Gears, hinges, and industrial components.
- Limitations: Hygroscopic (absorbs moisture), requiring pre-drying before printing.

Limitations of FDM 3D Printing
While FDM is versatile and cost-effective, it has certain limitations that manufacturers should consider:
1. Mechanical Properties
FDM-printed parts often lack the strength of traditionally manufactured parts, especially when under forces that pull layers apart. This necessitates over-engineering for load-bearing components. It is also impossible to predict part strength using conventional engineering tools, because of parts orthotropic properties (meaning force direction strongly affects part strength just like traditional composites).
Solution: Advanced tools like Slicedog® can optimize material usage by up to 50% and predict whether a part will withstand loads.
2. Resolution and Surface Finish
Due to the layer-by-layer nature of FDM, parts often have visible layer lines, making them less suitable for applications requiring a smooth or high-resolution finish.
3. Limited Automation
Most FDM printers require manual setup, part removal, and supervision. This limits scalability for high-volume manufacturing.
Applications of FDM 3D Printing
- Manufacturing
FDM is widely used for producing small-scale end-use parts and aiding in manufacturing processes. Applications include:
- Jigs and Fixtures: Custom tools for assembly lines.
- Spare Parts: Low-cost replacements for broken or hard-to-source components.
- End-Use Parts in Aerospace and Automotive: Lightweight, functional components.
- Print Service Providers
The competitive market of 3D print service providers serves industrial clients, with 70% of orders coming from manufacturing sectors. They specialize in 3D printing larger or more challenging print jobs.
- Education and Prototyping
Schools, universities, and R&D departments use FDM to teach engineering principles and create prototypes for testing.

3D printed prototype
Conclusion
FDM 3D printing is a versatile and cost-effective technology with applications in prototyping, low-volume manufacturing, and industrial tooling. While it has limitations, advancements in software and materials continue to expand its potential.
For manufacturers looking to integrate 3D printing into their workflows, FDM offers an accessible entry point with significant room for growth. Tools like Slicedog® can help overcome challenges like material optimization and strength prediction, enabling better results for industrial applications.
Optimize Your 3D Printing Today
Explore our solutions and learn how Slicedog® can revolutionize your 3D printing processes by saving 50% material and ensuring part strength. Contact us today for more information.
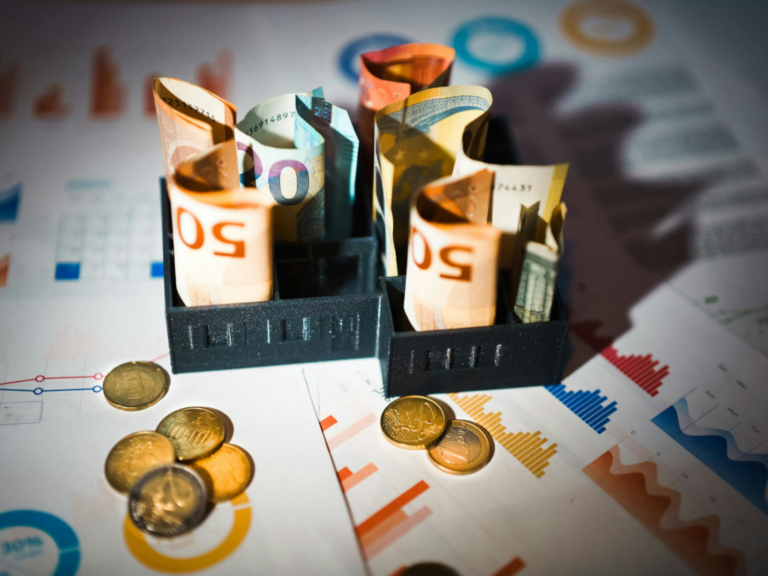